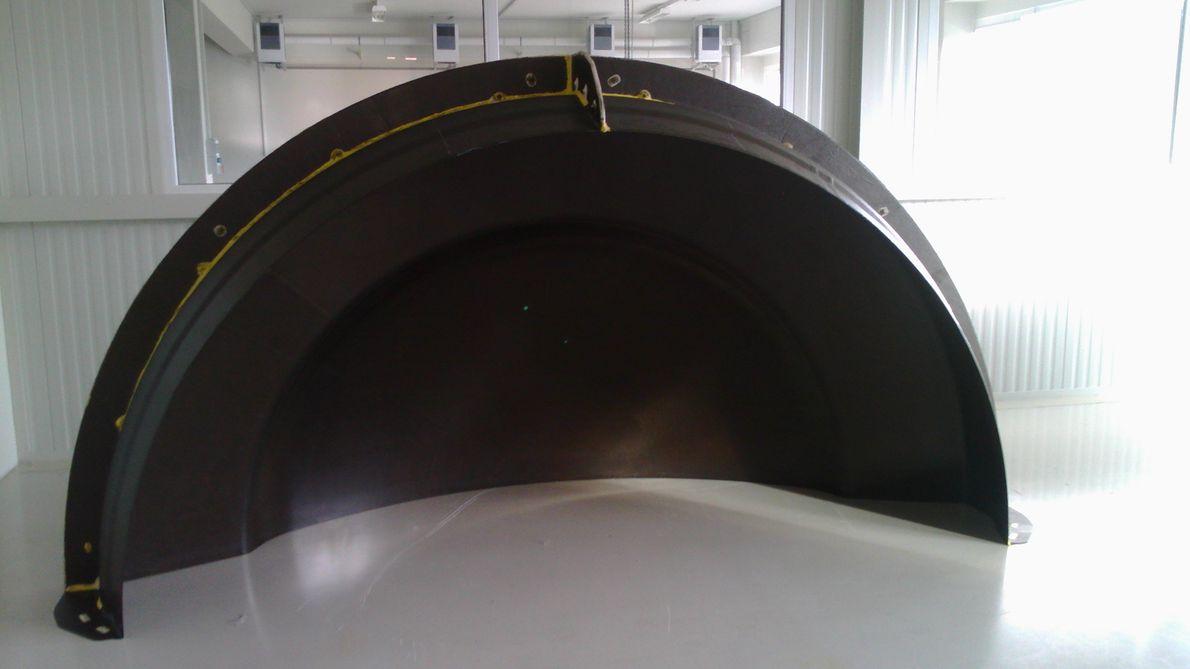
Depletion of resources and rising prices of traditional energy sources stepped up the quest for alternative sources with a heightened focus on planet-friendly, safe and renewable sources. While the use of Wind Energy dates back to 1850s, it witnessed mainstreaming in the 1970s. As its popularity grew, the demand for more efficient & cost-effective windmills rose. Epoxy-based composites triggered transformational advancements in turbine rotor blade technology. It led to optimal aerodynamic rotor blade architecture with greater dimension stability that maximized the amount of energy harnessed from the wind. Ability to meet stringent process & application demands, has made epoxy thermosets a material of choice for designers and manufacturers.
Composite Epoxy Systems offer a unique combination of excellent mechanical properties, endurance capability, performance and cost effectiveness. Wind blade manufacturers, globally, choose from an extensive portfolio comprising Resin Infusion Systems, Resin Systems for Prepregs, Tooling Systems, Gel Coats, Expandable Epoxy Systems, Adhesives and Hand Lay-up Systems. These versatile systems are suitable for different processes & blade designs and perform under static & dynamic loading.
Sustained R&D has enabled the Wind Industry to derive cutting-edge performance with our novel offerings like ultra-slow resin infusion systems, instant thixotropic structural adhesives, slow reacting-high strength adhesives and fast-curing adhesives for repair, among others. Our latest innovation, the multiple award-winning, patented technology Recyclamine allows epoxy thermosets which are now non-recyclable to be, recovered, reused & repurposed. This facilitates end-of-life recycling and zero-waste manufacturing, thereby plugging into a circular economy. For several industries, ecological, environmental and societal impacts of composite waste are, now, a thing of the past.
- Superior adhesion for a wide service range
- Outstanding toughness & stiffness
- Excellent static & dynamic load handling
- Uniform stress distribution across the structure
- Rapid strength build-up
- Excellent creep & shrinkage resistance
- High thermal resistance & conductivity
- Outstanding wettability & flow
- Fast, easy & complete impregnation of fibres
- Enables recovery & reuse of reinforcement
- CMR-free & VOC-free variants
- Non-toxic & DNV-GL approved variants
- Low initial mix viscosity
- Ultra-slow to fast reactivity
- Thixotropic nature
- Low exothermic heat even for thick sections
- Adjustable pot-life over a wide range
- Short de-molding time
- Ideal for large to extra-large components
- Suitable for varying environmental conditions
These are not common to all products within the portfolio. Choice of a product will depend on specific requirements for an application.